Innovation
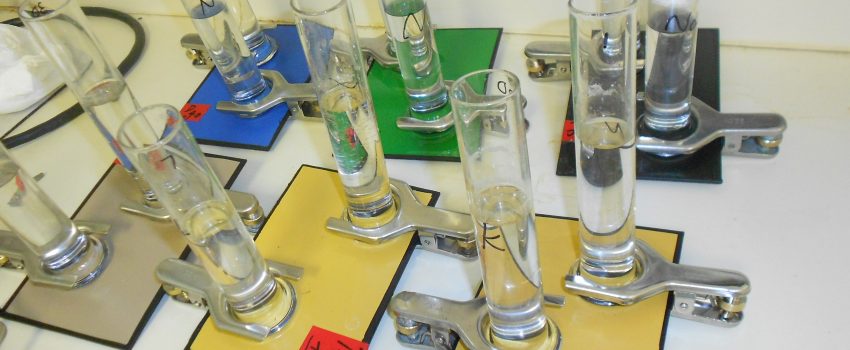
A combination of innovative technology and an agile commercialization process quickly and economically brings new products to market
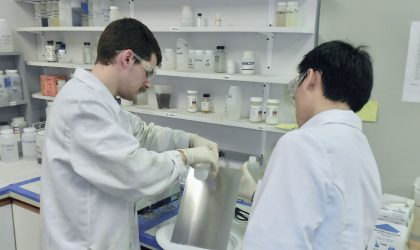
Technology
We follow a disciplined process that matches the cost and effort to the development stage.
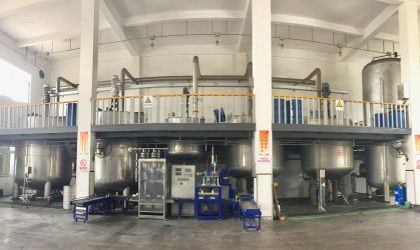
Commercialization
Ecosil uses long term relationships with partners and customers to rapidly commercialize innovative coating technologies.
Innovation can be seen as a science, an art, and even a sport. 15 years of developing innovative metal surface treatment products has taught the Ecosil team that collaboration between technical innovators, visionaries, investors, and marketers is needed to be successful. We have had the benefit of accessing seed funding and Small Business Innovative Research (SBIR) grants from federal agencies such as the National Science Foundation (NSF) and the US Department of Defense (DOD) to develop a product line with sales of over $5 million. We did this with debt and equity funding from a private manufacturing company, and by partnering with licensees in the US and a joint venture partner in China. This experience has motivated us to seek new technologies to commercialize in the surface modification of metals with the goal of improved part performance. We are prepared to offer equity to innovators and investors who partner with us.The following examples demonstrate areas where we are developing breakthrough technologies.
Innovation Example: Aluminide Diffusion Coatings For Wear, Corrosion and Oxidation Resistance
Ecosil has done extensive research on diffusion coatings with a goal to improve the wear and corrosion resistance of metal substrates including nickel-based super alloys, stainless steel, and high strength steel.
Aluminide diffusion coatings were produced in high strength steel (##) on a project conducted for the Air Force Research Laboratory to improve wear resistance. The goal of this effort is to replace current chrome plating on aircraft parts such as landing gear. The produced coating provided wear resistance close to that of hard chrome plated high strength steel, but corrosion resistance of the coating was not as good as chrome plated steel.
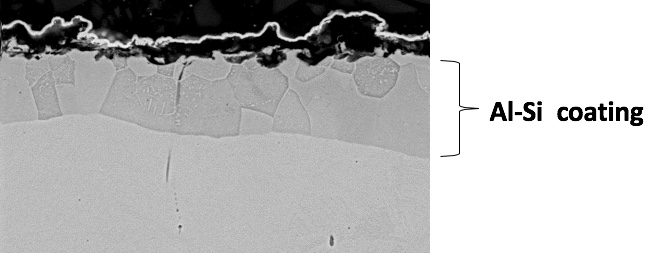
A novel process has been developed to apply aluminum and other elements such as silica to nickel superalloy used in jet engine turbines to create an aluminide diffusion layer in conjunction with a large aerospace company. The process has advantages over chemical vapor deposition, pack cementation, slurry, and thermal spray methods. It is non-line of site, produces a consistent coating thickness on complex shapes, and is water-based with no solvents. The process also has the capability of co-depositing multiple elements including metallic and non-metallic materials simultaneously.
Diffusion coatings of aluminum on 316 stainless steel were also produced to determine optimal coating composition and diffusion conditions to produce a consistent diffusion layer. The application for this coating would be compressor turbines used in marine applications for large ship propulsion.
Innovation Example: Plasma Coating
Plasma surface treatment
Ecosil can treat various solid materials with low temperature vacuum plasma deposition. This has been tested for coating powders, polymer membrane sheets and organic tire cord polymers. The plasma treatment applies a nano-coating that modifies the surface energy of the substrate. This can be done using various monomers, power levels and vacuum to create different surface characteristics such as water resistance (hydrophobicity), or permeability (hydrophilic). This video shows test plasma coating systems available at Ecosil used to coat solid particles, membranes and fibers.
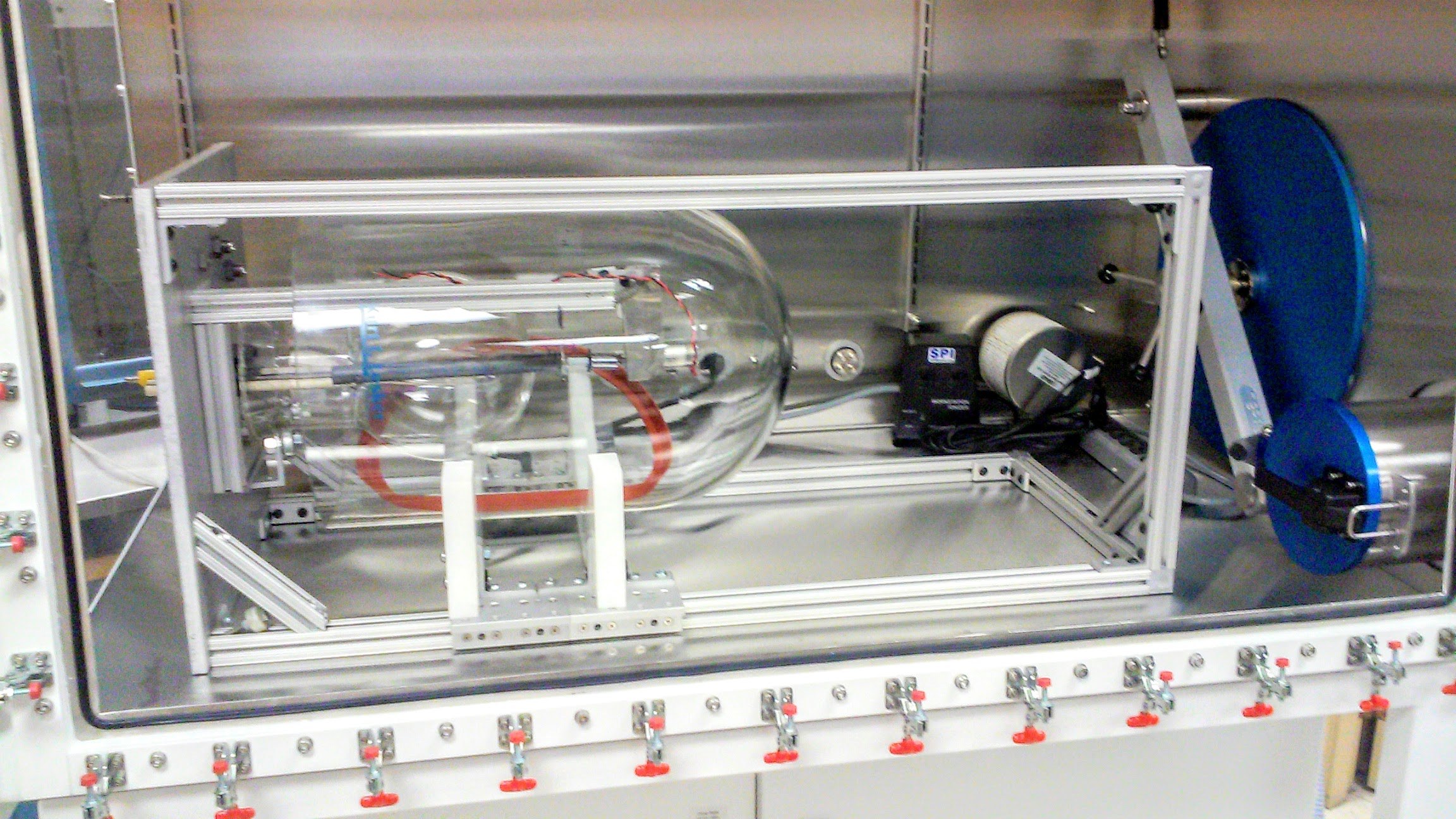
In one project Ecosil designed and built a laboratory scale vacuum plasma deposition system for a client to apply a very thin coating of silicon to the surface of metallic nano-particles. This system used a rotating process vessel to continuously expose solid particles to the plasma gas within the vessel. This design eliminates rotating seals used to maintain the vacuum. and creates and even coating with no “clumping” of particles together. Because the system was designed to conduct process testing for development purposes, it is capable of operating at various conditions of power input to the plasma system, gas flow rate of the coating element, rotational speed and direction of the agitation vessel, and processing time. Video at: